Gracias a un nuevo procedimiento de recubrimiento en seco, ya no se necesitan disolventes químicos y se elimina la parte de la fabricación de células que consume más energía. Con ello, PowerCo SE de Volkswagen ha desarrollado una nueva forma de crear baterías para VW y podría ahorrarle al fabricante de automóviles cientos de millones de euros cada año.
Aunque el proceso es un poco difícil de explicar, la empresa ha desarrollado un nuevo procedimiento de “recubrimiento seco” que permite fabricar electrodos de manera más rentable. Como explicó Volkswagen: “En la producción industrial moderna de electrodos, los materiales de las baterías se mezclan con aditivos líquidos y disolventes hasta formar una pasta. Luego se recubren con papel de cobre o aluminio, luego se secan y se calandran”. Este es un proceso costoso y que consume mucha energía, pero el recubrimiento seco elimina dos de los pasos.
Las baterías VW ahorran a la empresa cientos de millones
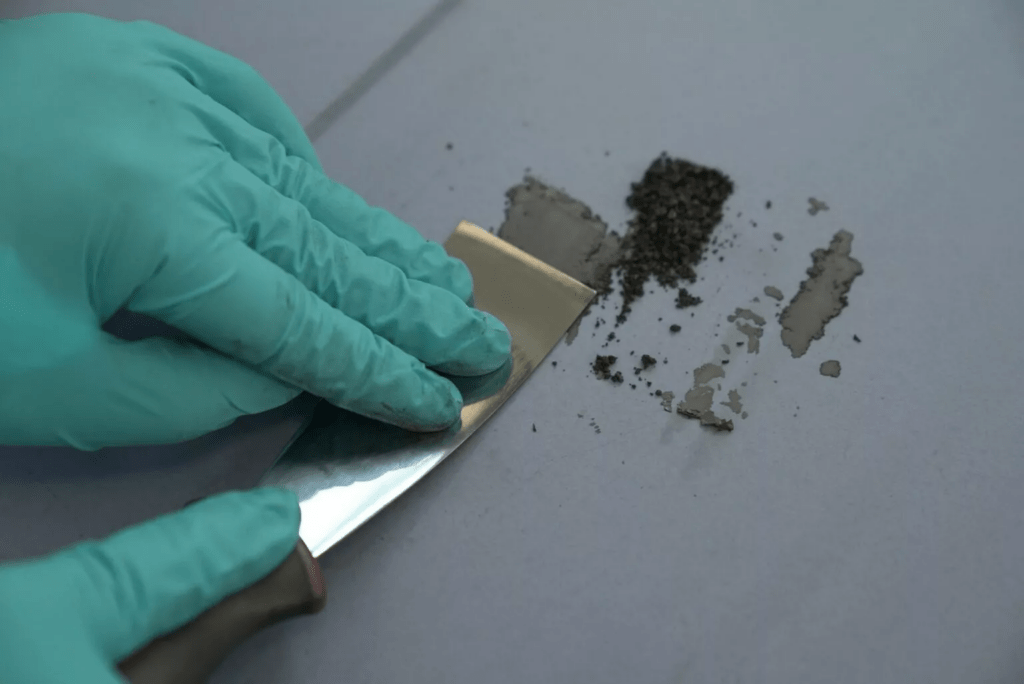
Ver más: Santa Fe 2024
En particular, el procedimiento de recubrimiento en seco permite "calandrar los materiales base en polvo directamente sobre la hoja, similar a un procedimiento de impresión". Volkswagen dijo que el recubrimiento en polvo se puede aplicar "extremadamente fino y uniforme" y puede ser tan fino como un mechón de cabello. El fabricante de automóviles dice que esto "garantiza una excelente densidad de energía espacial y un ciclo de vida prolongado, al tiempo que mejora la capacidad de carga rápida de la batería".
Todo esto está bien, pero el ahorro de costes es enorme, ya que ya no se necesitan disolventes químicos y se elimina la parte de la fabricación de células que consume más energía. Hablando de eso, el nuevo método puede generar un ahorro de energía de aproximadamente 30%. La producción también puede realizarse en fábricas que requieren 15% menos de espacio físico y esto amplifica los ahorros.
¿Cómo es esto posible?
Como señaló Volkswagen, “por cada bloque de construcción de una Gigafábrica normal con una capacidad de producción de 20 GWh, se pueden ahorrar cuatro líneas paralelas de recubrimiento y secado, lo que equivale a un área de 7.000 metros cuadrados (75.347 pies cuadrados). De este modo, la longitud exterior de la planta se puede reducir en unos 100 metros”. El fabricante de automóviles añadió: "Al no tener que utilizar hornos de secado y sistemas de aspiración que consumen mucha energía, se ahorrará energía equivalente al consumo anual de 40.000 hogares privados".
Frank Blome, director ejecutivo de PowerCo SE, no se contuvo cuando dijo: “Lo que la celda de estado sólido es para el producto, el revestimiento seco es para la producción: un verdadero cambio de juego. Si se amplía con éxito, nos dará una posición única en el mercado y ventajas competitivas definitivas”.
La empresa de baterías ya está probando y optimizando la tecnología en una línea de producción piloto en el norte de Alemania y planea introducir el nuevo proceso de fabricación en fábricas de Europa y América del Norte. Está previsto que el desarrollo finalice el próximo año y deberíamos ver la producción en 2026 o 2027.